Following on from the last post full of silliness...
While building the fore hatch I was also simultaneously building a new sliding companionway hatch. It is not completely made from G10 but it is close.
What happened is that old original companionway hatch blew off of the boat during a storm and disintegrated. I built a temporary out of luan and pine which has kept the boat dry but wasnt going to cut it for anything else. So I got the bright idea to build one and what follows is that process.
The old hatch has seen better days. Yes, that is six peices....
I wanted it to resemble the original as much as follows so I did some cyphering...
Traced the original fore and aft boards on G10. 3/8" for the aft and 1/4" for the fore.
Then I cut them to shape...kinda. I did some finer cutting after this picture was taken.
While that was going on, I also cut to length and striped in half a piece of 1-1/4"x1-1/4" G10 bar. The result was two 3/4"x1-1/4" bars and one very very tired table saw. Here they are...
I then took the four pieces out to the boat, clamped them in place, drilled the guide holes to assemble them by. Back at the boat yard...er...porch, I tapped the holes and assembled the frame using silicone brass screws. It is taking shape!
To stiffen it up I applied thickened epoxy on some of the joints and held it square using an impromptu jig.
Behold....
Next up was attaching a piece of oak 1/2"x3/4". This will allow a piece of plywood to be bent gently. Any thicker and it would interfere with the deck as it slides. Note the countersunk screws...
Back in the casa I let a cut to fit piece of 3/8" plywood relax for a few days in this position. I was very careful with my choice of plywood. It is not marine but it was expensive!
When I felt like it was ready, I epoxied it in place...on the top only...
LOOK AT IT! Thin coat on the wood...
Now for the underside...
BANG! Wood thinly coated...
Now back to the top. Two layers of 1708. Held down at the sides because it wrapped over to the G10 "runners" and didnt want to stay there. I applied some "discipline".
I love working with epoxy...
Best tool in my arsenal; Bar stool with a 24"x24" piece of plywood screwed down...get one!
This shit took forever. Every time I applied epoxy I had to let it fully set up because I was working during the day. I didnt have the luxury of applying the next coat or whatever in a few hours. The routine was epoxy, next day wash sand wash epoxy, next day wash sand epoxy blah blah blah. I was doing this for the fore hatch at the same time so it was a regimen of fore hatch today and companionway hatch the next and so on. I loved every single minute of it though.
Back to the story...here I have filleted in fairing filler on the bottom to smooth the transition caused by the oak stick. That is not just any old fairing filler though. It is the load bearing filler plus I poured the chopped glass to it. So before you cry babies complain...read the above!
And one layer of 1708 with a couple of neat coats...
Really super clean surface and really super chopped glass/colloidal synthesis to repair a cut imperfection...
After a night of drinking and thinking I realized that the height of the fore end of the hatch was too high...oh the irony! No seriously. I wish to have a seahood and my hatch will need to slide in the hood. So what do I do? I ground a 1/2" off of the fore end "board" like a boss!
and that is all I got done on the companionway hatch for the time being...
More to come....
Fair winds..../)
Check it
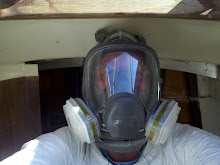
- Jimmy - The Skipper
- Florida flat-lander refitting an Alberg 30, hull #329, for an eventual circumnavigation of the globe and the journey of a lifetime before I get too old!
Friday, April 5, 2013
Companionway Hatch Construction
Saturday, March 30, 2013
Fore Hatch Construction
It has been quite a while since I have bloggity blog blogged! Well, let me limber up my fingers and get right to it. I am about to take you on a ride into the seedy underworld of solid epoxy experimentation and fiberglassing fantasy land! You will never be the same after reading this....because it is going to be a long read!
Another view...
And another with thickened epoxy curing in the corners to give it some stability.
Next up was to make something to epoxy my new frame to that would also be a seat for the new smoked lens. I was actually making all this stuff in a different sequence but I do not want to confuse you. So for the sake of the story I am simplifying it....or dumbing it down :)
Anyway, here is the makings of what I call "the lens seat".
I traced the new lens and then drew inner parallel lines. That is 1/4"x24"x24" G10 by the way...
Then I cut the exterior portions off. I used a 2x4 clamped in place as a guide and a tungsten grit blade in the jigsaw.
Then using a tungsten grit hole saw, I started the interior cuts. I bought a complete set of grit hole saws 3/4" up to 4". Cost is no concern for my baby! (but i have to say OUCH!)
After cutting from hole to hole, this is the result! I rounded the corners after this pic...
After playing around with the pieces I have so far I realize there is a design flaw...
I knew this was coming but I didnt know exactly how much was needed. You can see the gap there, its 3/8". So I set about stripping four pieces of 3/8" G10 and cut/trimmed to fit to beef up the lens seat piece. They are slightly smaller, or inset, so that there is room for filler later.
First two epoxied in place...
And the next two pieces overnight...who snuck the bud light cartons in my house?!?!?!?
With that done I could tack the other piece on. It was getting cold so I used 207 hardener. Trying to keep the neighbor's dog from pissing on it was a challenge.
I then applied a couple rounds of thickened epoxy on the inner part and used a heat lamp to help it along because it was getting cold outside. 50's...brrrrrrr
Over the next couple of weeks I filled the exterior portions, sanded, filled sanded, filled some more and sanded some more...except for the aft side. That was going to take some special attention due to it needing to be....different!
Check it out so far...
and...
and...
the G10 cutting/ripping station....
Next was addressing the aft side. I need it to be solid, well more solid than the rest because it will be drilled through and bear the weight of the hatch on hinges.
So what I did was carefully rip this piece of G10 to fit and then epoxy in place. I didnt get a picture of the rip but it is a sharp angle on top that allows it to fit inside where it looks ill fitting in this pic:
I then epoxied in place and filled the gaps on either side...
It turned out alright, up to this point anyway....
Lens in place...test fit
I did not take pictures of the fairing out part of the work. Here is a pic of it faired out and ready for painting.
I need to drill holes for the lens and the hinges yet but it is 90% complete structurally. See that thing behind it? That is the new companionway hatch which I made simultaneously along with the fore hatch.
I had to stop construction (and the refit) here (mid Jan) because something big has happened. It is good news and I will tell you my secret after I fully update the blog!
Fair winds...._/)
Ok. So my original forty five year old fore hatch was leaking and being held together by the lens screws. The lens was a clear one or at least twenty five years ago it was clear. It needed to be replaced.
See, its old and crappy.
Disgusting. But I am sure it was gorgeous back in the day.
The wood has lost a lot of meat.
Because I am a lazy bastard who doesnt want to be a slave to constantly varnishing, I decided to do something different, something I have never done before; I am going to make my own glass hatch!
BANG!
BANG! For the shape I striped 3/16" G10, carefully cut to length. I held them away from the hull with 3/16" chair leg pads. That is not the real name for the pads but I have been drinking...felt lamp pads whatever. They are there to allow room between the hatch and deck for gaskets on the sides.
I glassed these together, in place, to form the beginnings of the best fore hatch in the history of Kentucky! This is the fragile result:
Another view...
And another with thickened epoxy curing in the corners to give it some stability.
Next up was to make something to epoxy my new frame to that would also be a seat for the new smoked lens. I was actually making all this stuff in a different sequence but I do not want to confuse you. So for the sake of the story I am simplifying it....or dumbing it down :)
Anyway, here is the makings of what I call "the lens seat".
I traced the new lens and then drew inner parallel lines. That is 1/4"x24"x24" G10 by the way...
Then I cut the exterior portions off. I used a 2x4 clamped in place as a guide and a tungsten grit blade in the jigsaw.
Then using a tungsten grit hole saw, I started the interior cuts. I bought a complete set of grit hole saws 3/4" up to 4". Cost is no concern for my baby! (but i have to say OUCH!)
After cutting from hole to hole, this is the result! I rounded the corners after this pic...
After playing around with the pieces I have so far I realize there is a design flaw...
I knew this was coming but I didnt know exactly how much was needed. You can see the gap there, its 3/8". So I set about stripping four pieces of 3/8" G10 and cut/trimmed to fit to beef up the lens seat piece. They are slightly smaller, or inset, so that there is room for filler later.
First two epoxied in place...
And the next two pieces overnight...who snuck the bud light cartons in my house?!?!?!?
With that done I could tack the other piece on. It was getting cold so I used 207 hardener. Trying to keep the neighbor's dog from pissing on it was a challenge.
I then applied a couple rounds of thickened epoxy on the inner part and used a heat lamp to help it along because it was getting cold outside. 50's...brrrrrrr
Over the next couple of weeks I filled the exterior portions, sanded, filled sanded, filled some more and sanded some more...except for the aft side. That was going to take some special attention due to it needing to be....different!
Check it out so far...
and...
and...
the G10 cutting/ripping station....
Next was addressing the aft side. I need it to be solid, well more solid than the rest because it will be drilled through and bear the weight of the hatch on hinges.
So what I did was carefully rip this piece of G10 to fit and then epoxy in place. I didnt get a picture of the rip but it is a sharp angle on top that allows it to fit inside where it looks ill fitting in this pic:
I then epoxied in place and filled the gaps on either side...
It turned out alright, up to this point anyway....
Lens in place...test fit
I did not take pictures of the fairing out part of the work. Here is a pic of it faired out and ready for painting.
I need to drill holes for the lens and the hinges yet but it is 90% complete structurally. See that thing behind it? That is the new companionway hatch which I made simultaneously along with the fore hatch.
I had to stop construction (and the refit) here (mid Jan) because something big has happened. It is good news and I will tell you my secret after I fully update the blog!
Fair winds...._/)
Subscribe to:
Posts (Atom)